Where MIM Differs from PM?
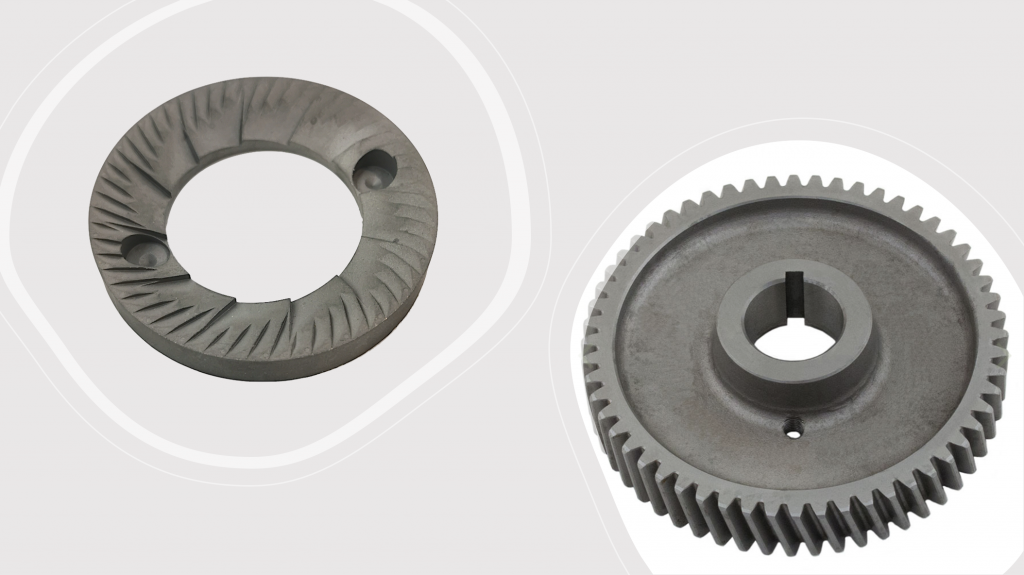
It is usually confused MIM with traditional press-sinter powder metallurgy (PM). The standard powder metallurgy forming step relies on vertical axis compaction to press a coarse powder into compact. The pressing route is the same as used to form pharmaceuticals pills. Die compaction is best at forming squat shapes that are easily ejected from the tooling while the ejection step requires the sides be parallel, a restriction in geometry not seen in MIM.
The major difference in the two technologies is in the final density and final properties. Because of friction between the powder and tooling, pressed powder is non-uniform. If sintered in a high temperature like MIM sintering cycle, the component would warp, like a potato chip. Thus, PM parts are lightly sintered and retain considerable porosity and have significant property degradations.
For PM , it uses larger powders versus MIM and to sinter at lower temperatures for shorter times to avoid distortion during sintering densification, resulting in lower properties. As an example, MIM strengths are about two-fold higher than PM, fatigue strength is more three-fold that of PM, and impact toughness is eight-fold higher when compared to PM.
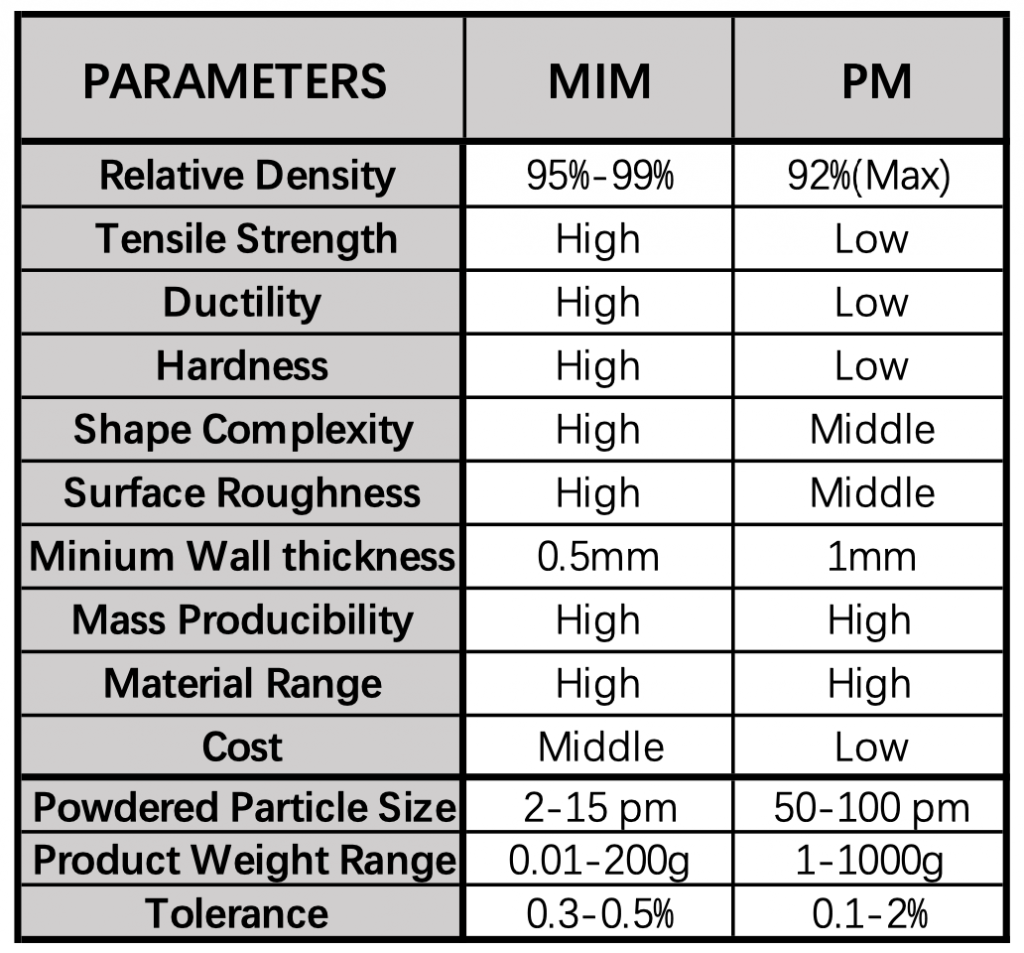
Where Does MIM Fit?
Considering saving cost , PM may be a cost-effective alternative for simple parts while MIM can produce parts with complicated geometries to eliminate secondary operations when it comes to high-density, high-complexity components that cannot be made by any other manufacturing process ,
Additional savings are found when you consider materials, design, assembly and logistic benefits to the MIM process, especial when the two or more subcomponents made by other production processes are combined into one single MIM component.
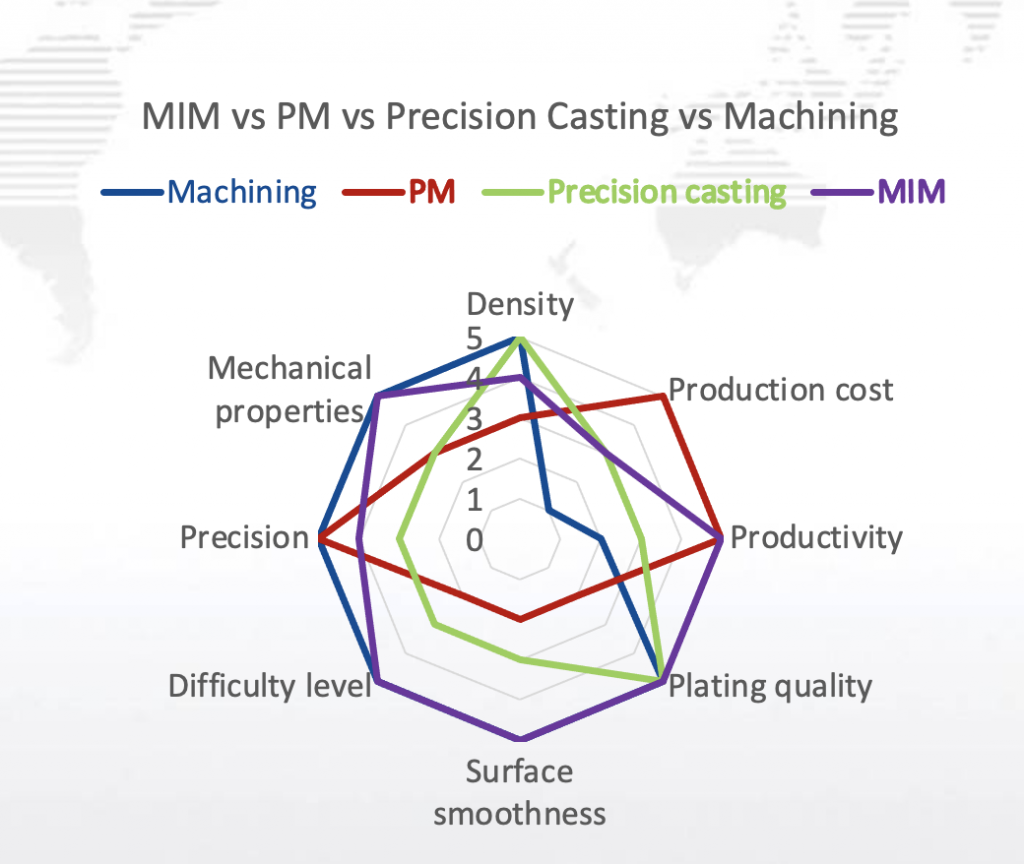
On every project, we aim to deliver more consistent parts, more efficiently, at lower costs. We discuss with customer and decide the material , change the design to reduce the weight ,revise the drawing to do away with the expenses associated with secondary processes such as machining, achieving net-shape in one time.
If you have such inquiry , our technician will be glad to discuss with you . Feel free to contact us and send email by alina@tcc-casting.com