Purchasing investmet casting is a very professional job, it is necessary for purchaser to understand related technical knowledge of investment casting, and fully communicate with foundry engineers. This article we list out some main points of purchasing precision investment castings for buyers.
I. Select an Investment Casting Foundry
To obtain high quality investment castings, it will require joint efforts and close collaboration of both sides (supplier & purchaser). Buyers need to spend a certain amount of time to develop suppliers before purchasing castings. Except to choose a reliable investment casting supplier, communication between the purchaser and foundry is very important before the design of investment castings. Therefore, purchasers and suppliers should focus on establishing long-term and mutually beneficial cooperation and good interactive relationship.
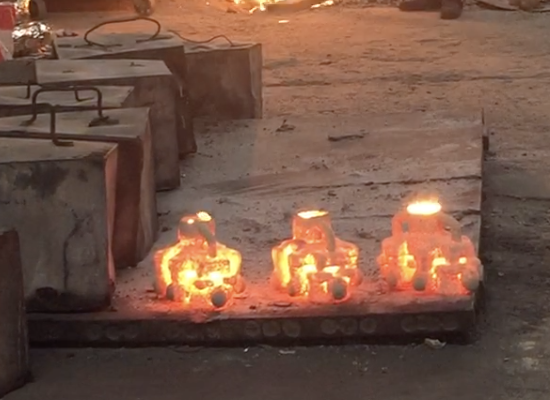
Currently, there exsit two kinds of different production processes of investment casting. One is water glass casting process, a kind of paraffin & stearic acid pattern material with water glass shell technology. The other is silica sol casting process, with high quality medium temperature pattern material, the whole silicon sol shell, and medium frequency induction melting quick pouring process. Cost of water glass casting process is low, but the size accuracy and surface roughness is relatively poor. It is mainly used to produce carbon steel and low alloy steel castings, and is difficult to produce a high level of investment casting. However, silica sol casting process can produce parts in high dimensional accuracy and good surface quality. It can reach or even exceed international level of investment castings. So, casting purchasers must first understand the foundry production technology and detection methods, then to determine if the foundry can achieve expected quality requirements for investment castings. Also need to know the production scale and management level about the foundry, thus to ensure on time delivery of bulk orders for qualified castings.
II. Focus on the Process of Investment Casting
One of the prominent advantages of investment casting is the flexibility of the structure design. So, the casting buyer should first learn the design knowledge of the investment casting process .The structure of the parts should comply with the requirements of investment casting, which will be easy to mold release, shell making, filling and cleaning, and also try to achieve uniform wall thickness. This will benefit for establishing a good temperature distribution and the solidification order, avoiding shrinkage cavity caused by local overheating. At the corner of the part, the designer should design appropriate casting round corners, to facilitate the filling, cooling and deoxidization. Especially in new product design, engineers who are familiar with casting process should participate in, so as to make casting design and material selection more reasonable, easy to guarantee casting quality, and can reduce the cost of investment castings.
III. Inquiry & Quotation
Buyers when sending a RFQ to investment casting foundry, should try to accurately explain in detail about material and technical quality requirements, such as the required machining sections, locating datum, heat treatment, surface treatment, packaging requirement, inspection and test items and the inspection report, etc. The annual requirements of the castings, the quantity of each order, and the place of delivery shall be provided. It is best to provide the weight of castings to facilitate the foundry quotation. The delivery cycle and payment terms are also important factors to be considered, which should be stated at the time of inquiry or quotation. Requirements about the casting quality should be economic, applicable and reasonable, on the premise of meet the use function, higher requirements will increase the difficulty of manufacturing, may also affect the production cost and price, this is not good for both purchaser and foundry.
ISO8062 has ruled the tolerance grade sequence of casting sizes, but no provisions shall be applicable to the investment casting precision grades. Steel castings generally choose CT4 – CT8, but CT5 is for small size less than 50mm. It will be hard to meet such accuracy if the size is larger than 100mm.So buyers need to consider the size of the casting when using ISO8062 standard.The American association of investment casting (ICI) and the German investment casting association (VDG) respectively made the tolerance standard of investment casting, which can be used as the reference of size tolerance for exported investment castings. ISO2768 is the tolerance standard for metal machining process, can be used as the general tolerance of investment casting machining. It is not suitable in some drawings that make ISO2768-mk as the general tolerance of casting directly, but for the some precision castings with size of less than 60mm, it is ok to meet such standard.
IV. Drawing Providing
Part drawing is the main quotation and production basis, enough information can help to avoid misunderstanding. Detailed drawings should clearly show the part name, material, tolerance, surface roughness, critical dimensions, permitting the residual gate height, processing base, processing surace and the machined surface, modify content, inspection requirements, heat treatment and surface treatment requirements, etc. We suggest casting purchasers to map casting and finished machining drawing seperately. When the customer has requirement on internal gate location, parting surface and the plunger position, shall specify the location of the position or not allowed to set in the drawing. For irregularly shaped complex castings, 3D drawing should be provided, which will be better for foundry to correctly understand drawings and make casting mold.
V. Mould and Sample Confirmation
Production of investment casting starts from the mold design and manufacturing, mold production cost is generally listed in the quotation alone, is a one-time cost, and should be paid by the purchaser in advance. Of course, mould ownership generally belongs to the purchaser, can be preserved and used by the foundry, but both sides should reach an agreement at the start dealing for the mould.
Due to the need of process, when foundries need to modify the original drawing design, they should map casting or separately write amendments to purchaser for confirmation, then to make mold.
After the mould is ready, foundry need to provide samples to purchaser first to check the size, assembly, or do the necessary testing. Only after passing testing of the sample, can the buyer start mass production. Sometimes it is not very convenient to modify some sizes, for those out-of-tolerance dimensions that will not affect use function, customers can directly use and don’t require to modify mould. In this case, it is better to ask customer to modify the drawing tolerance according to actual samples, or written note when confirming sample, in order to avoid dispute when mass production in the future.
Afrer checking the drawing or sample, when the design is modified, proper mold fixing fee will be charged. So before making mould, purchasing party shall carefully review the drawings and keep good communication with the manufacturer.
Sample material generally should be consistent with drawings requirements, when it is difficult to make sample in required material, foundry should negotiate with buyer in advance. After getting agreement with the customer, foundry can use another kind of material with silimar or same shrinkage rate, but the sample will be only to used to check the size and geometry shape. Again when mass production, drawing material is applied.
When the mould is tranferred from a foundry to another foundry, due to the using of different wax materials, shell materials and technological conditions, that may cause the change of the shrinkage rate, it is necessary to reconfirm the sample before bulk production.
VI. Production Order
Before placing production order, purchasers should confirm if below issues have been implemented:
1. After mold making, many dimensions of castings will be guaranteed by mold, foundry may pay attention to only a few important sizes when mass production. Purchaser needs to clear state the key control size, surface requirement and acceptance criteria.These key information will help to control the quality during production and improve the production efficiency.
2. Order in advance. Investment casting is different from mechanical processing, it is also different from die casting and other casting processes. During investment casting process, there are lots of auxiliary process, so the production cycle is long, it will require around a week time from wax injection, the shell making to pouring. Castings with holes or blind holes will need longer shell making drying time. Insufficient drying time will cuase the poor quality of casting surface and even the casting scrap. After pouring, also needs enough time for cooling before before moving to cleaning process. So buyer should issue a purchase order with guaranteed time to secure on time delivery.
Any casting inquiry consider ordering in China? Pls contact us with email alina@tcc-casting.com.