What is Sand Casting?
Sand casting, is a metal casting process by using sand as the mold material. So it is also called sand molded casting. The term “sand casting” can also refer to a metal part produced via the sand casting process. Professional factory that produces sand castings are called sand casting foundry. Currently, nearly 60% of metal castings are produced via sand casting process.
Sand casting is relatively cheap and sufficiently refractory even for steel foundry use. Besides the sand, we will also mix a suitable bonding agent (usually clay) with the sand. The mixture is usually moistened, typically with water, but sometimes with other substances, to develop the strength and plasticity of the clay and to make the aggregate suitable for molding. The sand is typically placed in a system of frames or mold boxes known as a flask. The mold cavities and gate system are created by compacting the sand around models, or patterns, or carved directly into the sand.
Basic Steps of Sand Casting Process
Pattern making
To start sand casting process, pattern making is the first step. The pattern is a replica of the exterior of the casting with dimensional allocation for shrinkage and finishing. If the casting is to be hollow, additional patterns called cores are used to create these cavities in the finished product. Patterns are usually made of wood, plastic, metal, or plaster; however, other materials or combinations of materials are used if there are additional specific properties required of the pattern. The number of castings to be made from the mold and the specifications required of the finished casting are two of the criteria that determine which material is selected for the creation of the pattern.
Core making
Next, making cores in the process. Cores are formed which are placed into the mold to create the interior contours of the casting. They are typically made of a sand mixture- sand combined with water and organic adhesives called binders- which is baked to form the core. This allows the cores to be strong yet collapsible, so they can be easily removed from the finished casting. Since cores are made in molds, they require a pattern and mold, called a core box. The core pattern is made in the same fashion as the casting pattern, but the core box is created from a durable material like metal or wood. Since the cores are made of sand, the mold cannot also be made of sand.
Molding
Molding is the multi-step process in which molds are created. In horizontal casting, the mold is contained in a two piece frame, called a flask. The upper portion of the flask is called a cope and the lower portion is a drag. First, molding sand is packed into a flask around the pattern. After the pattern is removed, gating and runner arrangements are positioned in the drag half of the mold cavity and the sprue is placed the cope portion. Gating systems are necessary for the molten metal to flow into the mold cavity. Cores are also placed in the drag portion of the mold if they are needed. To finish the mold, the cope (top) section is placed on the drag (bottom) section, and the mold is closed and clamped together. In our foundry, molds are created in large automated molding machines (Disamatics), a process which warrants its own detailed explanation.
Melting & Pouring
Melting is the preparation of the metal for casting, and its conversion from a solid to a liquid state in afurnace. It is then transferred in a ladle to the molding area of the foundry where it is poured into the molds. After the metal has solidified, the molds are vibrated to remove the sand from the casting, a process called shakeout.
Cleaning
Cleaning generally refers to the removal of all materials that are not part of the finished casting. Rough cleaning is the removal of the gating systems from the casting. Initial finishing removes any residual mold or core sand that remains on the piece after it is free of the mold. Trimming removes any superfluous metal. In the last stages of finishing, the surface of the casting is cleaned for improved appearance. In addition, at this point, the casting is inspected for defects and adherence to quality standards. This inspection may include non destructive testing to determine whether the part will adequately perform for its intended use.
Types & Methods of Sand Casting
Precoated sand Casting
Precoated sand casting is a relatively recent invention in molding techniques for mass production and smooth finish; it was first used by Germany during the Second World War. The molding material is a mixture of dry, fine silica sand with minimal clay content and 3-8 percent thermosetting resin (phenol formaldehyde or silicon grease). When the molding mixture drops on to the heated pattern plate, a hard shell of around 6 mm thickness is formed. In order to cure the shell completely, it must be heated to 440 to 650°F (230 to 350t) for several minutes.
Precoated sand casting is the most precision casting process compared to other two sand casting methods, very close to investment casting, so it is many used for small metal casting.
Resin sand casting
Aplication of resin sand coating during sand casting process can be as isolated layers between rough castings and the sand mould. This will avoid the burnt-on sand problems, protect the metal water from oxidization at high temperature, prevent the bad chemical reaction between cast shell and hot steel water.
Such resin sand coating can also help to absorb the nitrogen factors, sulphur factors and carbon factors, thus to increase the properties of the sand castings. This kind of sand casting method can be used for castings with rough surface requirement and low unit cost.
Green sand casting
Green sand casting is a common sand casting process using green sand as the molding material. Green sand does not mean sand in green cloor,but is a kind of wet quartz sand in the sense that it is used in a wet environment. The mold is made by ramming prepared sand around a pattern, held in a flask. The patterns are withdrawn, leaving the mold cavity into which metal will be poured. Molds are made in two halves, an upper portion, the cope, and a lower portion,the drag. The boundary between cope and drag is known as the parting line.
Cores, made from sand bonded with resins and baked to give sufficient strength, may be supported within the mold cavity to form the internal structure of hollow castings. Chills of various designs may be embedded in the mold cavity wall to control the solidification process.
Risers are reservoirs of molten metal used to ensure that all regions of the casting are adequately fed until solidification is complete. Risers also act as heat sources and thereby help promote directional solidification. Molten metal is introduced into the mold cavity through a sprue and distributed through a system of gates and runners. Green sand casting is usually for large steel castings.
Advantages of Sand Casting:
- Sand castings impose few restrictions on product shape. The only significant exceptions are the draft angles that are always needed on flat surfaces oriented perpendicular to the parting line. With good patterns and tooling, the proper choice of molding sands and careful foundry practice, surprisingly intricate details can be reproduced in this manufacturing process.
- Dimensional control and consistency in sand castings ranges from about ±0.030 to ±0.125” (± 0.8 to 3.2 mm) depending on the size and design of the parts being cast. Within this tolerance range, the more generous tolerances apply across the parting line.
- Surface finish ranges between approximately 300 and 500 gin (7.7 – 12.9 gm) rms. Various surface finishes can be applied: Shot blast finish, painted, powder coated, plated (chrome and others),
ect. - Sand castings are relatively inexpensive compared to investment casting or die casting processes. The process is quite simple and most any metals can be used. Parts can be used as it is or can be machined.
- Sand castings are acceptably precise and above all, highly versatile. This process can be applied to simple shapes as well as castings of considerable complexity, and it can be used with all metals such as cast and ductile irons, copper alloys, steel alloys, stainless alloys, and other complex metals.
- Sand casting can lend itself to both low volume and high volume production.
When should you choose sand casting?
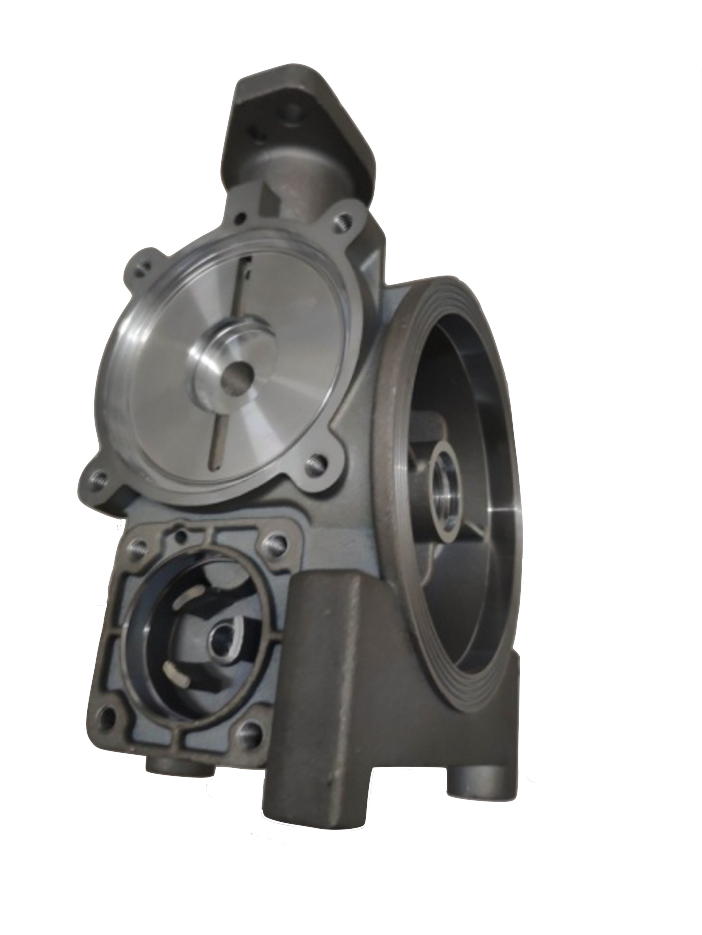
Sand casting is an economical process for creating rough metal parts. Raw castings are then machined to produce finished products or components. Sand casting is the least expensive of all casting processes, including die and investment casting. Sand casting may require a longer lead time for production at high output rates (1–20 pieces/hour/mold), but is unsurpassed for large-part production. Sand has almost no upper limit on part weight and minimum part weight ranges from 0.075–0.1 kg. The sand is bonded together using clays or chemical binders. In most operations, the sand can be recycled many times, requiring the addition of only small amounts of sand each time.
Preparation of the sand mold is fast but requires a pattern that can “stamp” out the casting template. Typically, sand casting is used for processing low-temperature metals, such as iron, copper,aluminum, magnesium, and nickel alloys. It can also be used for hightemperature metals where other means would be impractical. Sand casting is by far the oldest and best understood of all techniques. As such, automation can easily be adapted to the production process, although somewhat less easily to the design and preparation of forms.
Thus, sand casting is a ideal casting process when you have a design for below requirements:
- Low tooling costs
- Low or high volume requirements
- Low part cost
- Quick delivery or turn around
Application Tip: Sand castings generally have a rough surface, sometimes with surface impurities and surface variations. A machining finish allowance is made for correcting these kinds of imperfections.
TCC Sand Casting Foundry
Whatever steel castings, iron castings or aluminum castings, TCC can always provide a good sand casting solution for you. Contact us to get more information on how our sand casting service can match your project requirements.