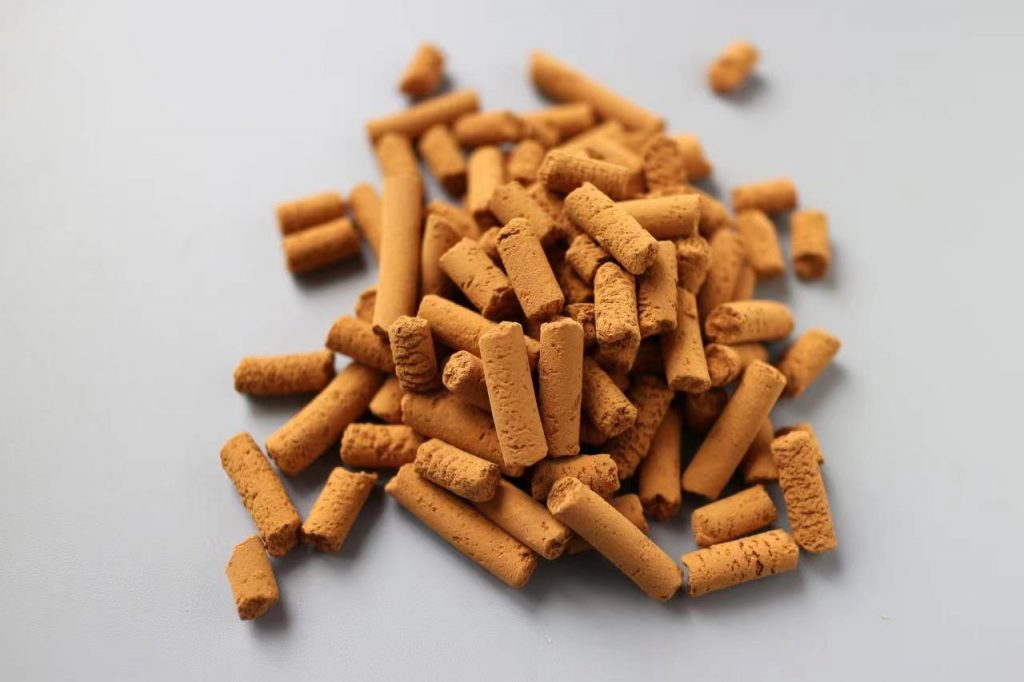
1. Saturated sulfur capacity: greater than or equal to 600 mg/g
2. Industrial sulfur capacity: 20%~35%
3. Penetrating sulfur capacity: more than 30%
4. Desulfurization accuracy: generally less than 0.05PPM
Uses: For the removal of H2S in various gases such as urban pipeline gas, water gas, semi-water gas, coke oven gas, steel mill raw material gas, biogas, petrochemical and other gases.
Features:
1. High desulfurization accuracy: when the imported H2S is 1000ppm, the export H2S is 0.05ppm, which is 20 times higher than the desulfurization accuracy (1ppm) of ordinary Fe2O3;
2. Fast reaction speed: the air velocity of 1000-20000h-1 is 3-6 times higher than that of ordinary Fe2O3;
3. Large working (penetration) sulfur capacity: under the conditions of 1 and 2, the one-time fine H2S sulfur capacity is 20%-25% when O2 is contained, which is 3-6 times that of ordinary Fe2O3 desulfurizers.
4. Good strength and good water resistance. Boiled in water for 2 hours or soaked for 30 days without pulverizing or mudding, and the strength remains unchanged after soaking in water and drying.
5. Wide applicable temperature range, it is better below 100℃
1. Filling
- Filling with grain suction machine
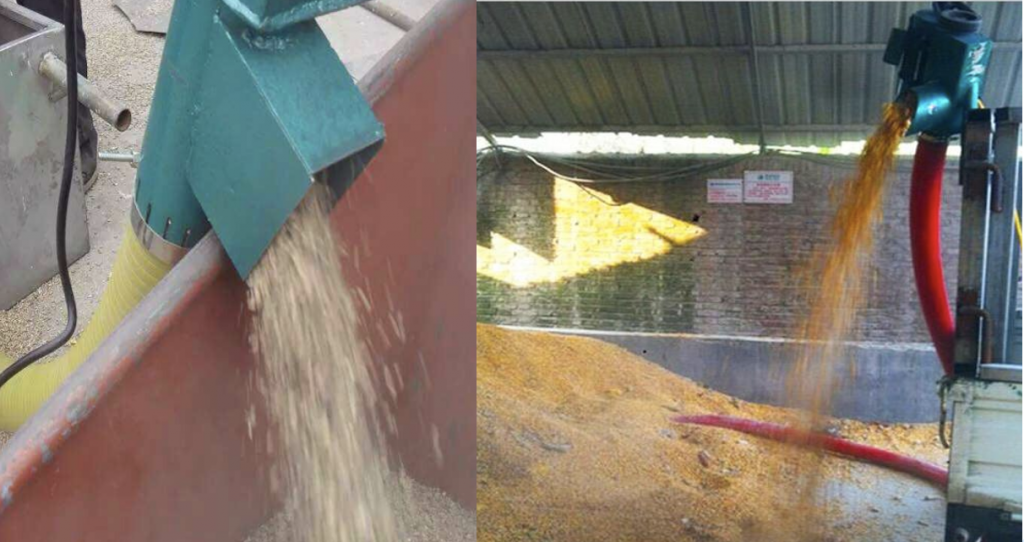
2. Hoisting and filling with a crane
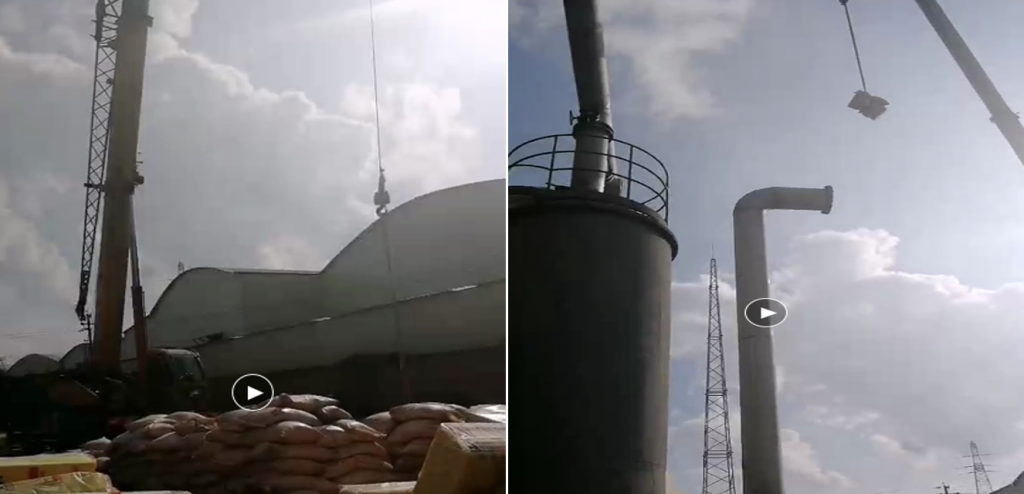
3. Hoisting and filling with electric hoist
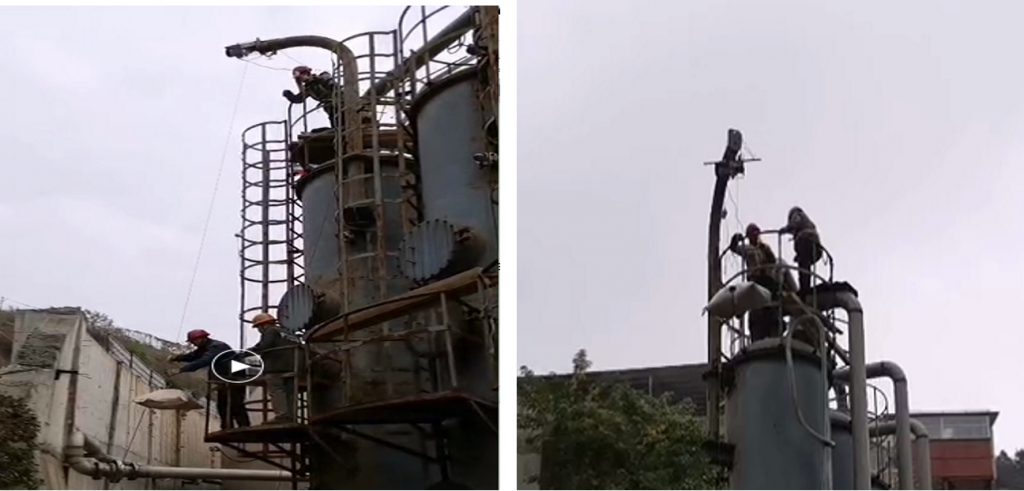
The quality of the desulfurizer filling directly affects the use effect, and it must be paid enough attention. The entire desulfurizer filling process should be in charge of a special person, and the following points should be paid attention to:
1) Lay two-layer meshes smaller than 8-10 mesh stainless steel mesh on the grate board of the desulfurization tower.
(2) Lay another layer of 20-30mm, Φ20-30mm thick porcelain balls on the wire mesh.
(3) Since dust will be generated during transportation and loading and unloading, it needs to be screened before loading.
(4) Using special filling tools, the discharge pipe should be able to rotate freely, so that the material can be evenly filled around the reactor, and it is strictly forbidden to pour the desulfurizer from the middle to prevent uneven filling.
(5) The strength of the desulfurizer increases with the increase of the amount of sulfur absorbed during the use process, so it should be packed in layers in the desulfurizer. Each layer is marked according to the filling height of the desulfurizer to ensure full, level and even filling.
(6) During the filling process, it is strictly forbidden to step on the sulfur agent directly. The wooden board can be placed on the material layer, and then enter the material and check the filling situation.
(7) At the inlet of the desulfurization raw material gas, a grid plate or crushed coke block should be installed to prevent the desulfurization agent from being blown away.
2. Use
(1) The desulfurization tower generally does not need to be specially heated and consumes energy, but the outdoor desulfurization device must be kept warm in winter to prevent the gas from being overcooled, reducing the activity of the desulfurizer and the accumulation of water on the bed and worsening the operation.
(2) Try to remove tar and water before desulfurization.
(3) The desulfurizer can be replaced all at once, or it can be replaced segment by segment according to the direction of airflow.
(4) Regularly discharge the water in the water separator in front of the desulfurization tower and the bottom of the desulfurization tower, and it is strictly forbidden for the gas to enter the desulfurization tower with liquid.
(5) The operation should be stable and the use should be reasonable in order to exert its excellent performance.
3. Clean up
1. Wet cleaning
①Close the inlet and outlet pipeline valves of the desulfurization tower before cleaning, (three desulfurization towers are alternately cleaned to ensure that there are desulfurization towers that can be used normally during the operation).
② Open the manhole at the top of the tower and inject water into the desulfurization tower. The water level is based on the submerged desulfurizer, and the soaking time is more than 8 hours.
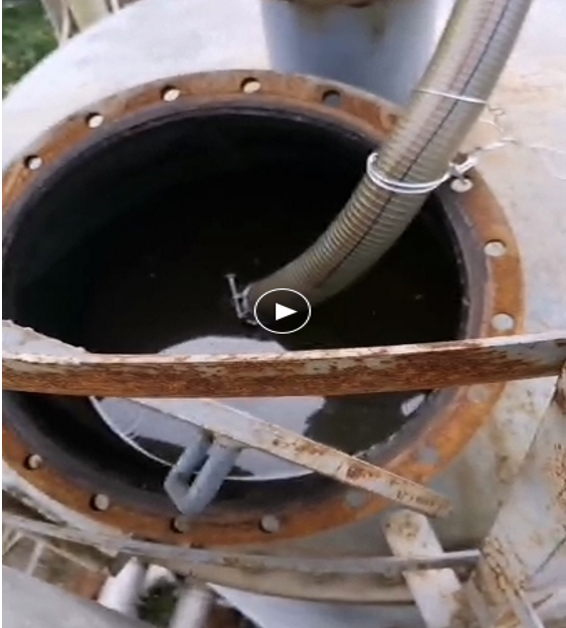
③ Drain the soaking water in the tower from the drain at the bottom of the desulfurization tower, first take out the desulfurizer in the lower layer of the desulfurization tower, and then take out the desulfurizer in the upper layer.
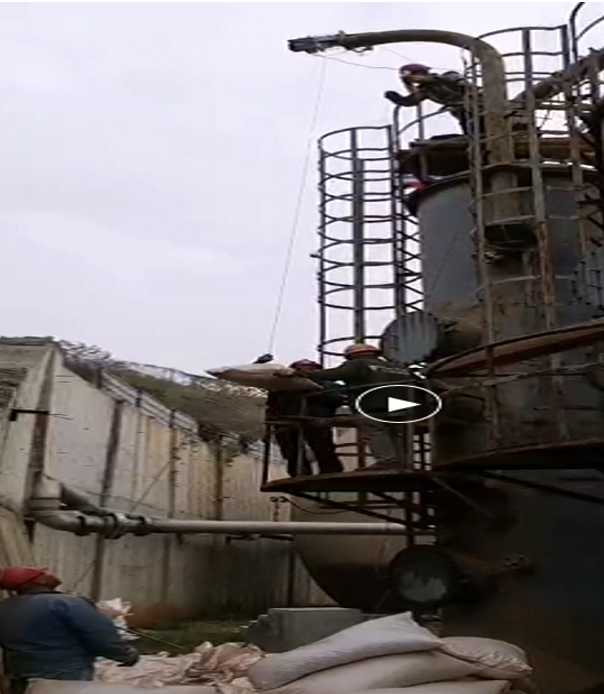
④ On-site must be ventilation, operators wear gas masks or long-tube ventilators. Monitor the concentration of hydrogen sulfide and combustible gas at any time on site.
⑤ Clean out the waste desulfurizer, lay it flat on the ground to dry, and then bag it (woven bag with inner film) to monitor the temperature of the desulfurizer after bagging to prevent spontaneous combustion.
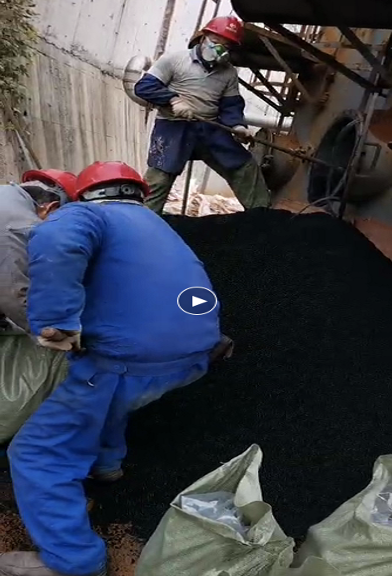
⑥ Loading and shipping.
2. Dry cleaning
①Close the inlet and outlet pipeline valves of the desulfurization tower before cleaning, (three desulfurization towers are alternately cleaned to ensure that there are desulfurization towers that can be used normally during the operation).
② Open the manhole in the lower layer of the desulfurization tower, take out the desulfurizer with tools, and monitor the site environment.
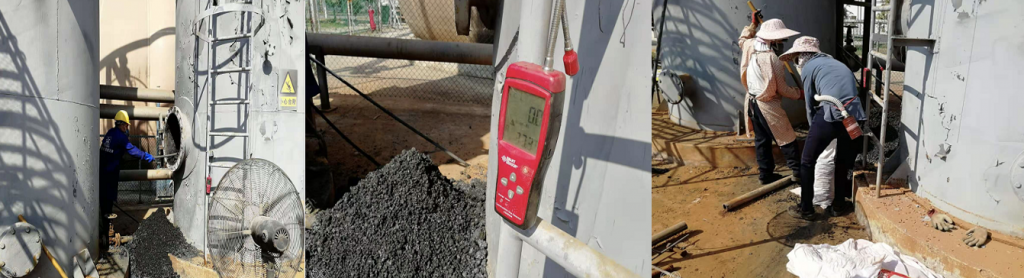
③ On-site filling, on-site forced ventilation, operators wear gas masks or long-tube ventilators, and monitor the concentration of hydrogen sulfide and combustible gas at any time.
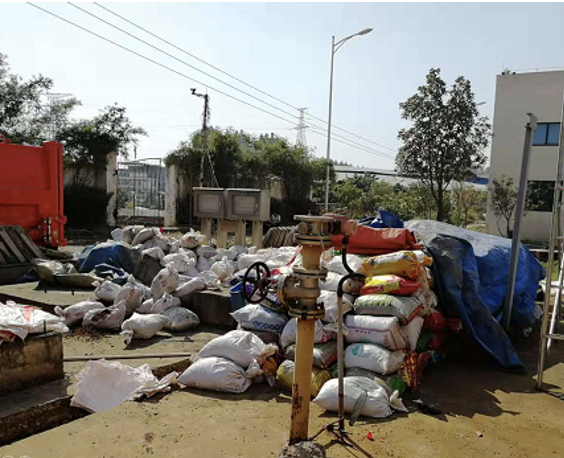
④ Pack the bag, monitor the temperature of the desulfurizer, and prepare for fire extinguishing in the event of spontaneous combustion.
4. Gas replacement
The use of inert gas to replace the biogas in the desulfurization tower was not used due to cost issues.
[contact-form-7 id=”1022″ title=”Message”]