Metal Powder injection molding (MIM) is an effective way to produce complex and precision-shaped parts from a variety of materials. This process produces parts for 50% less than the cost of CNC machining or casting. MIM is able to produce parts with complex shapes, superior strength and excellent surface finish with high volume manufacturing.
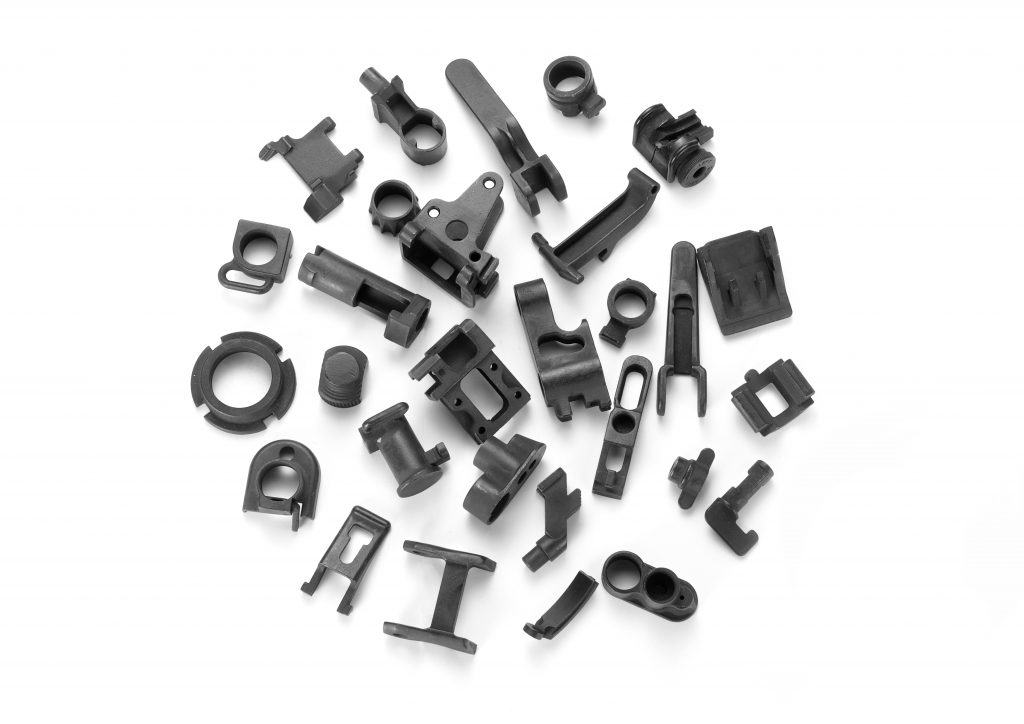
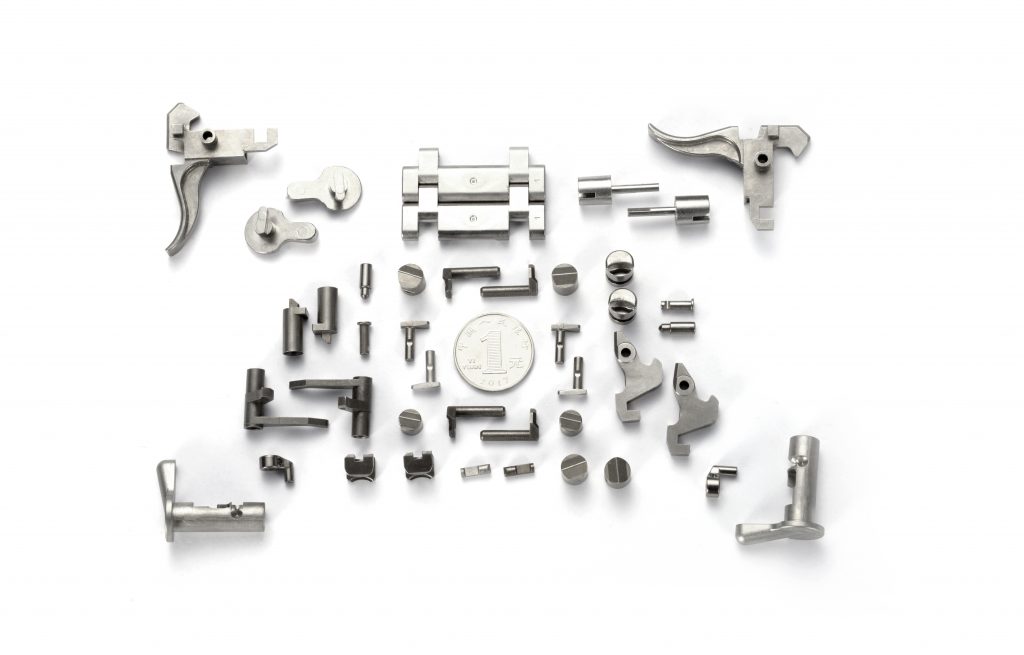
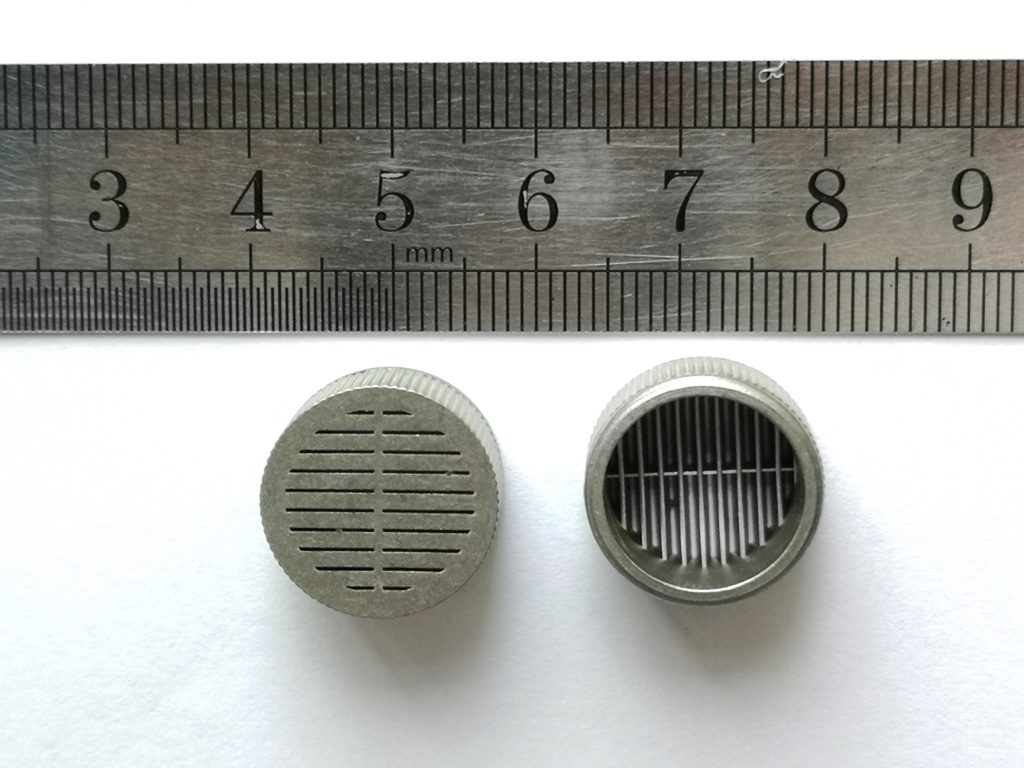
Metal Powder Injection Molding(MIM)–Forming Process
MIM’s technology not only has less conventional powder metallurgy technology process, no or less cutting cutting cutting, high economic benefit, but also overcomes the traditional technology of powder metallurgy products low density low, uneven texture, mechanical performance, not easy forming thin-walled, after the shortcoming of complex structure, especially suitable for mass production of small metal parts, complex and has special requirements.
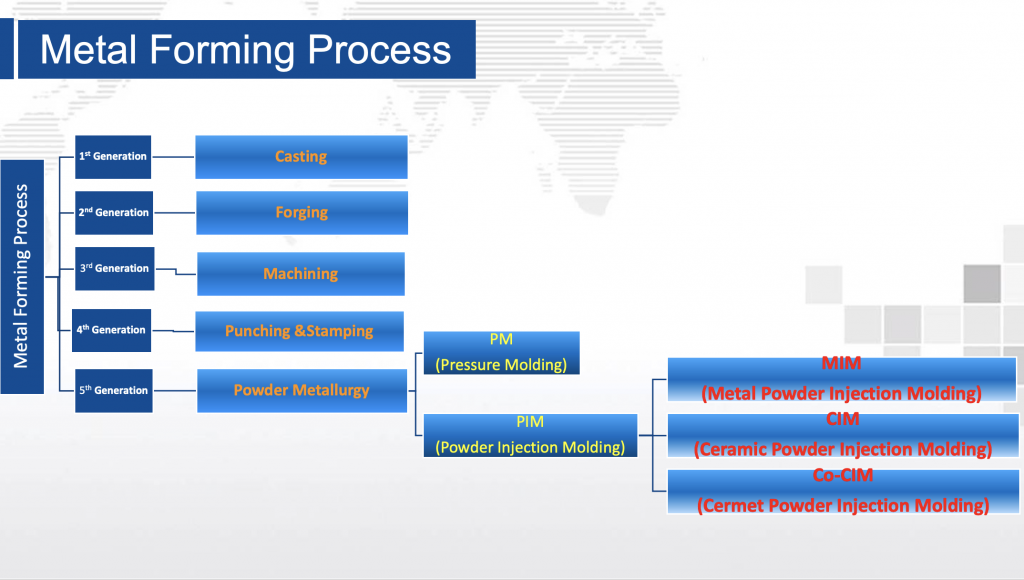
Metal Powder Injection Molding(MIM)- Working Flow
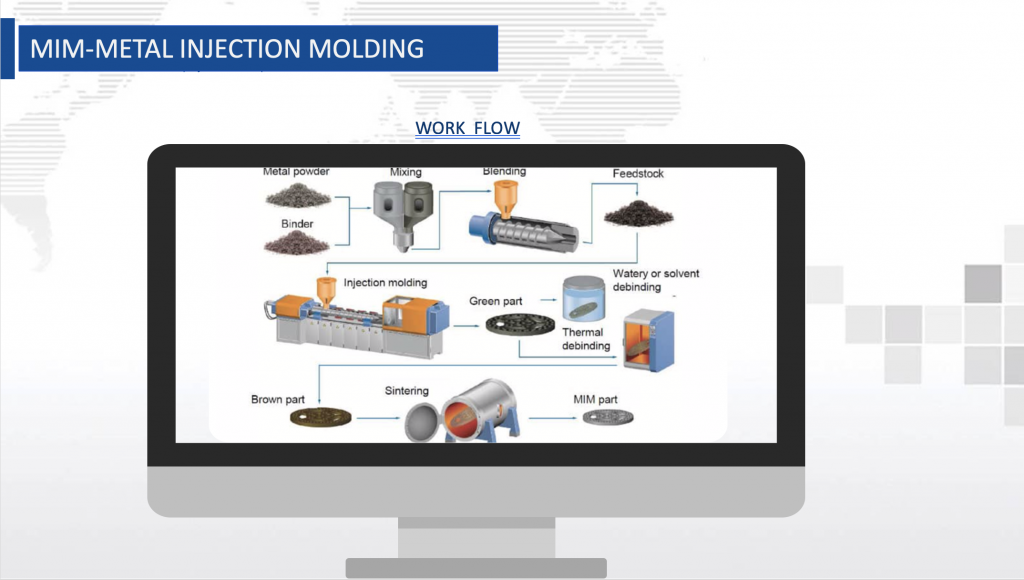
Feedstock preparation – The first step is to create a powder mixture of metal and binder. The powder metals used here are much finer (typically under 20 microns) than those used in traditional powder metallurgy processes. The powder metal is mixed with a hot thermoplastic binder, cooled, and then granulated into a homogenous feedstock in the form of pellets. The resulting feedstock is typically 60% metal and 40% binder by volume.
Injection molding – The powder feedstock is molded using the same equipment and tooling . However, the mold cavities are designed approximately 20% larger to account for the part shrinkage during sintering. the feedstock is melted and injected into the mold cavity, where it cools and solidifies into the shape of the part. The molded “green” part is ejected and then cleaned to remove all flash.
Sintering – This step is to sinter the “brown” part in a high temperature furnace (up to 2500°F) in order to reduce the empty space to approximately 1-5%, resulting in a high-density (95-99%) metal part. The furnace uses an atmosphere of inert gases and attains temperatures close to 85% of the metal’s melting point. This process removes pores from the material, causing the part to shrink to 75-85% of its molded size. However, this shrinkage occurs uniformly and can be accurately predicted. The resulting part retains the original molded shape with high tolerances, but is now of much greater density.
After the sintering process, no secondary operations are required to improve tolerance or surface finish. However, just like a cast metal part, a number of secondary processes can be performed to add features, improve material properties, or assemble other components. For example, a MIM part can be machined, heat treated, or welded.
Metal Powder Injection Molding(MIM)-Application Area
MIM process are found in numerous industries, including aerospace, automotive, consumer products, medical/dental, and telecommunications. MIM components can be found in cell phones, sporting goods, power tools, surgical instruments, and various electronic and optical devices.
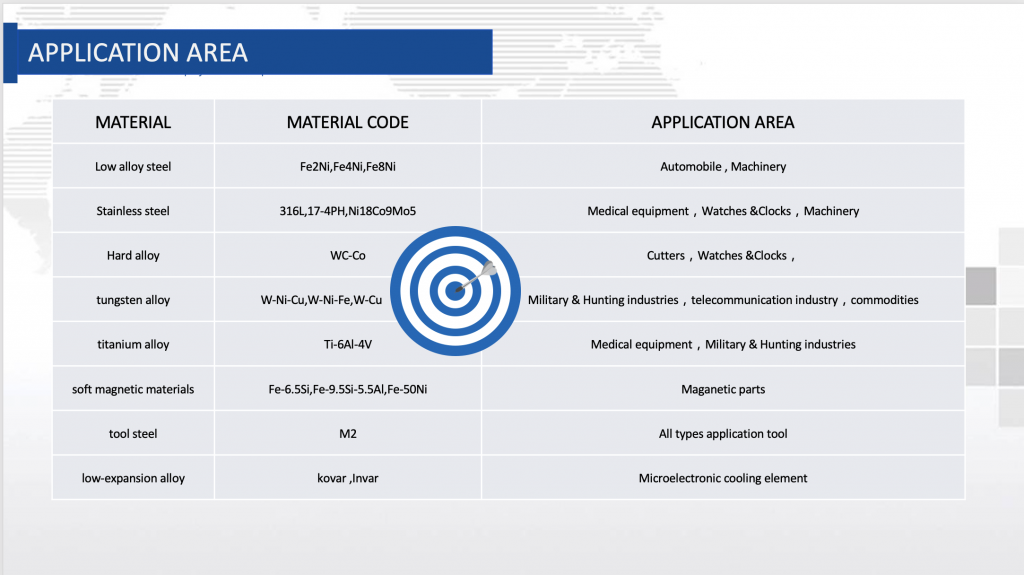
Metal Powder Injection Molding(MIM)– Compare to other technics
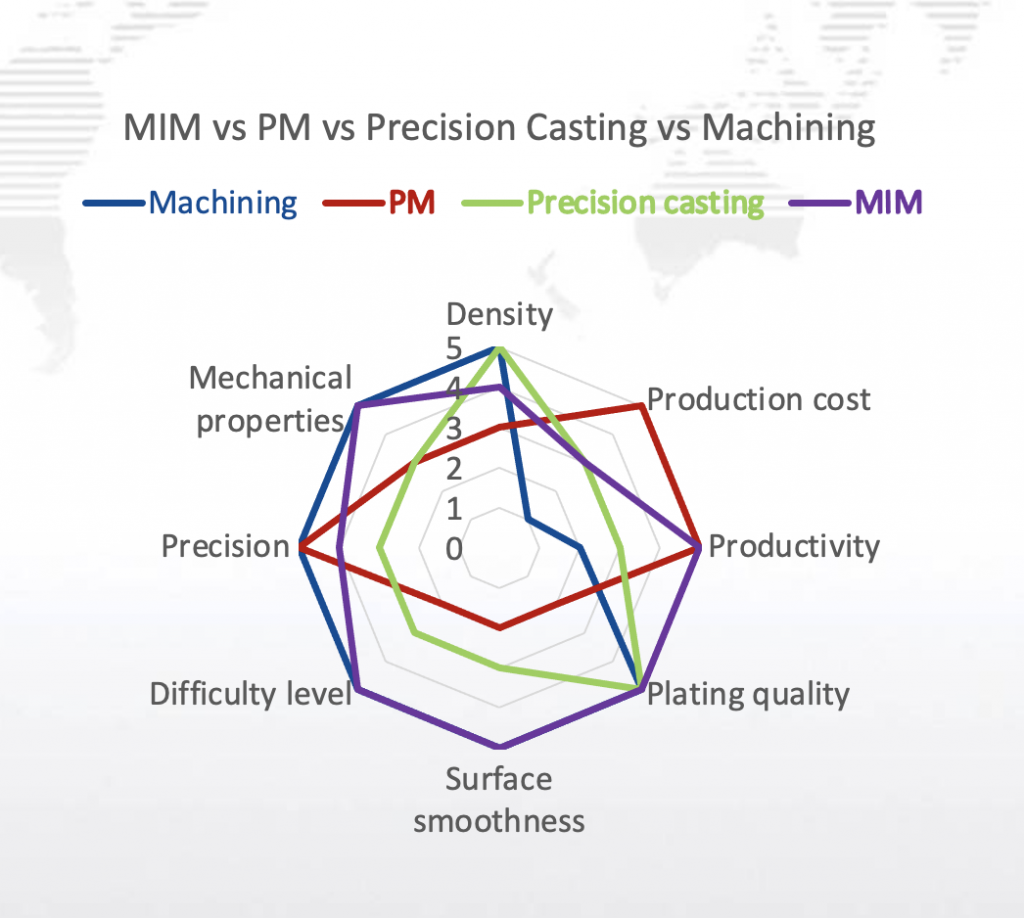
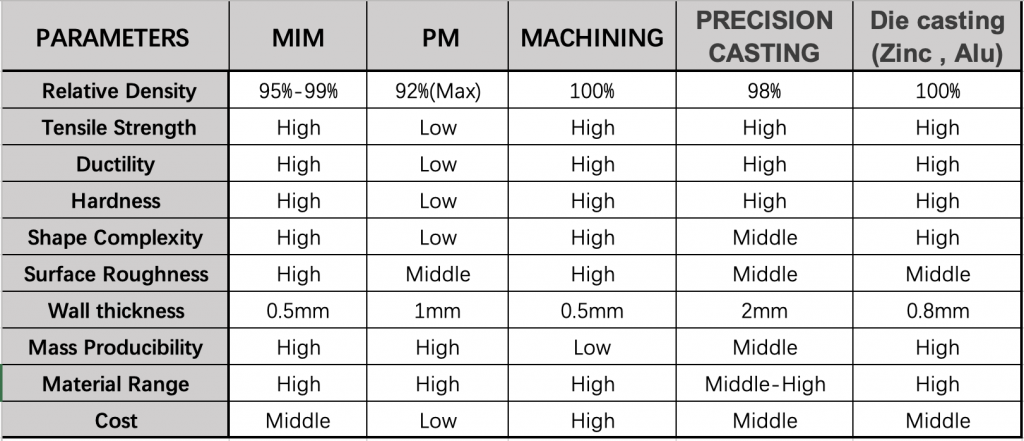
For more information on metal injection molding and to determine if MIM is the best process for your part run, please feel free to contact TCC by email : alina@tcc-casting.com