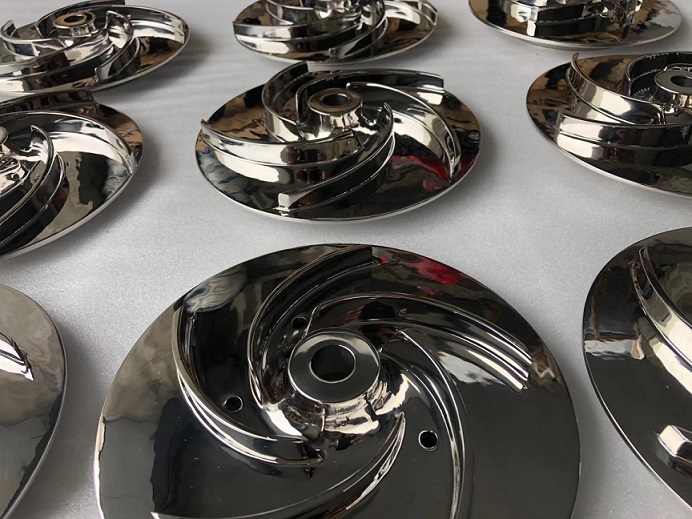
Most people have seen stainless steel castings at some point in their lives. They have likely seen cast stainless steel parts used in a wide variety of products, from kitchenware to medical instruments, yet few realize why so many designers prefer stainless steel castings.
One of the most valuable assets of stainless steel castings is its resistance to corrosion. Lower grades of stainless steel castings can withstand corrosion in water environments and basic atmospheric conditions. And higher grades of stainless steel castings can withstand corrosion caused by acid and alkaline solutions.

Stainless steel castings contain several alloying elements that are in line with the specific composition and grade. We can divide stainless steel castings into several general classes: austenitic stainless steel castings, ferritic stainless steel castings, martensitic stainless steel castings, duplex stainless steel castings, and precipitation hardened stainless steel castings. The distinction between each class is based primarily on the predominant phase present in the stainless steel castings as determined by the major alloying elements.
Effects of Alloying Elements on Stainless Steel Castings
1. Manganese: Adding manganese to stainless steel improves hot working properties and boosts toughness, strength, and hardness.
2. Nickel: Nickel can help produce stainless steel castings that are incredibly ductile, corrosion resistant, and tough at both high and low temperatures.
3. Chromium: Stainless steel parts with higher percentages of chromium have a higher resistance to oxidation than parts with lower percentages of this alloying element.
4. Carbon: Carbon, along with iron, is the major alloying element that is used to make stainless steel. It is also used to increase the hardness and strength of the metal.
5. Copper: This alloying element enhances the corrosion resistance and formability of the stainless steel castings. Copper can also be added to decrease work hardening in grades designed for improved machinability.
Choose Stainless Steel Casting for Your Next Project
We can well understand that alloying elements can have major effects on stainless steel castings. Now that you know the effects that common alloying elements have on stainless steel castings, it’s time to determine the best option for your specific needs. TCC Casting is a leading supplier of quality stainless steel investment castings to major companies throughout the world and can provide you with the exact component you are looking for. Contact us to discuss your next project!