What is Precision Casting?
Precision casting, also called investment casting, is a lost wax casting process widely used for producing ferrous and nonferrous metal parts. Unlike other casting processes, precision casting produces net shape parts with excellent surface finish and dimensional accuracy. This manufacturing process is ideal for applications that have relatively low production quantities (100 to 10,000 pieces) or rapidly changing product designs.
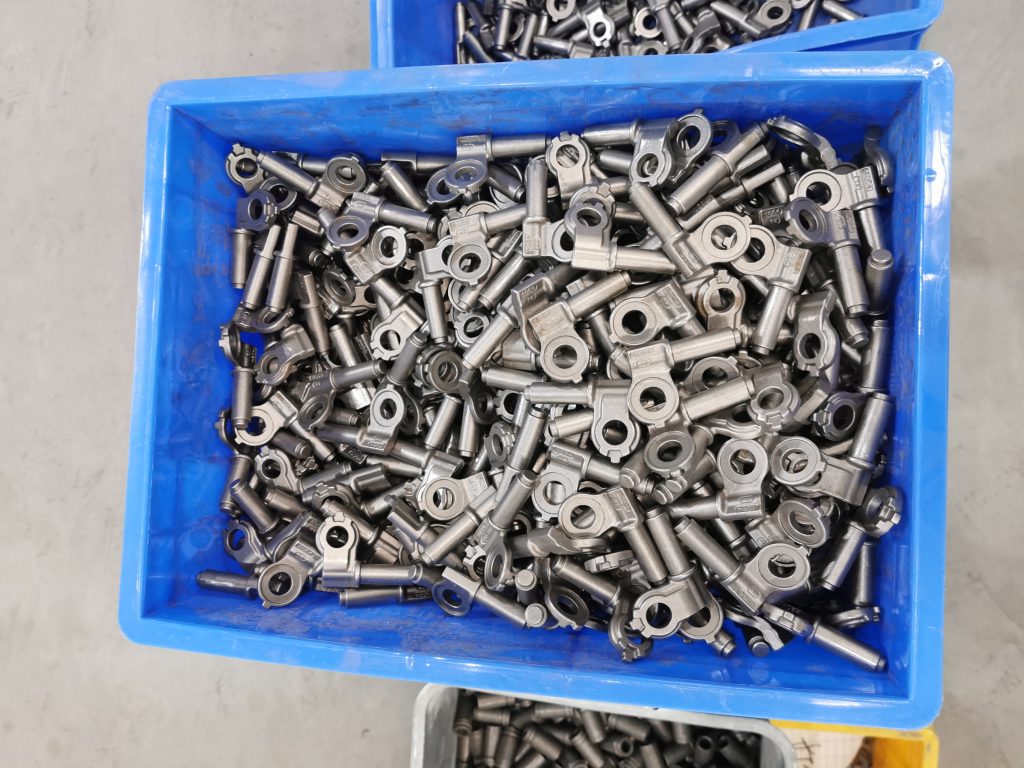
With precision casting, we can cast nearly 200 alloys. These metals range from ferrous—stainless steel, tool steel, carbon steel and ductile iron—to non-ferrous—aluminum, copper and brass. When cast in vacuum, super alloys are also available. The only process that matches this breadth of materials is machining, but it cannot produce the complex geometries that precision casting can deliver.
Since precision casting uses expendable patterns and ceramic shells, it is excellent for complex and detailed part designs. The process manufactures intricate parts that are difficult, if not impossible, to machine, forge or cast. Examples include internal passages and ports in a valve body, curved vanes of an impeller and internal cooling channels in a turbine blade.
The critical barrier in prototype development and short-run production is the time and cost for injection molds. Each precision casting requires one wax pattern, and these patterns are injection molded. As design complexity rises, the tooling often becomes too costly and too time consuming to make prototyping and low-volume production practical.
Precison Casting Process
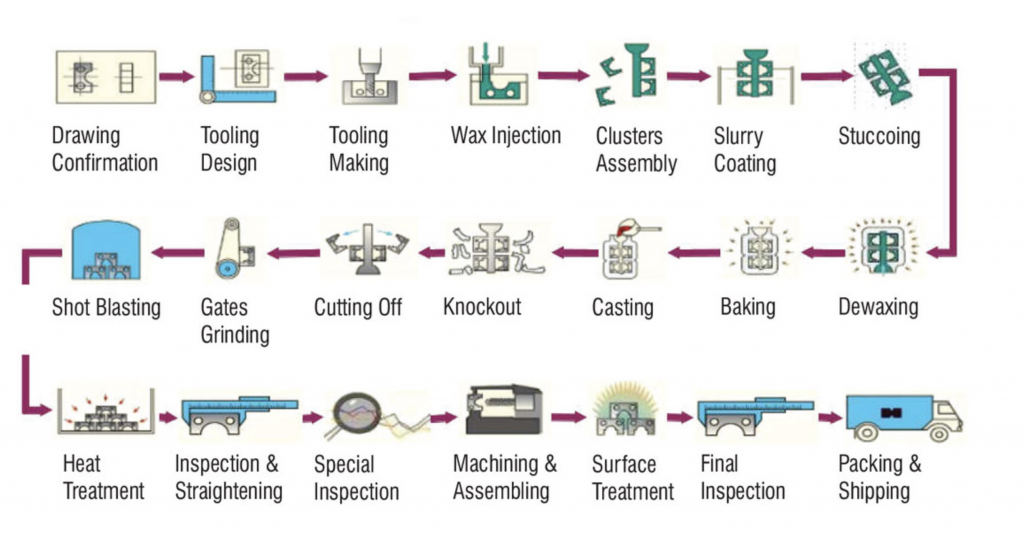
Generally , it has below steps
PRECISION CASTING WAX INJECTION
The precision casting process begins with fabrication of a sacrificial pattern with the same basic geometrical shape as the intended finished cast part. Patterns are normally made of precision casting wax that is injected into a metal wax injection .
WAX PATTERN ASSEMBLY
Fabricating the injection die can often require several months of lead time. Once a wax pattern is produced, it is assembled with other wax components on a central wax stick, called a sprue, to form a casting cluster or
assembly
SHELL BUILDING
The entire wax assembly is then dipped in a ceramic slurry and covered with a sand stucco , and allowed to dry.
DEWAXIN
The dipping and stuccoing process is repeated until a shell of 6-8 mm (1/4-3/8 in) is applied. Once the ceramic has dried, the entire assembly is placed in a steam autoclave to remove most of the wax and the remaining amount of wax that soaked into the ceramic shell is burned out in a furnace
CASTING & POURING
At this point, all of the residual pattern and gating material is removed, and the ceramic mold remains. The mold is then preheated to a specific temperature and filled with molten metal, creating the metal casting
KNOCK OUT
Once the casting has cooled sufficiently, the mold shell is chipped away from the casting .
CUT OFF
Next, the gates and runners are cut from the casting .
FINISH
After minor final post processing (sandblasting, machining),the castings are complete and ready for shipment .
Manufacturing of Precision Castings
Precision castings are made in our lost wax investment casting method. The production process of preicision castings includes injecting wax into patterns to form wax model, building tree assembling by sticking each wax model, creating ceramic shell layer, pouring metal liquid into sprue gate, building a perfect shape like the wax pattern. Mostly, precision casting is the only solution for a new designed parts for its high accuracy, free dimensions, smooth surface, and complex shapes. And precision casting is economically manufactured for the low pattern cost.
Why Precision Casting from TCC casting?
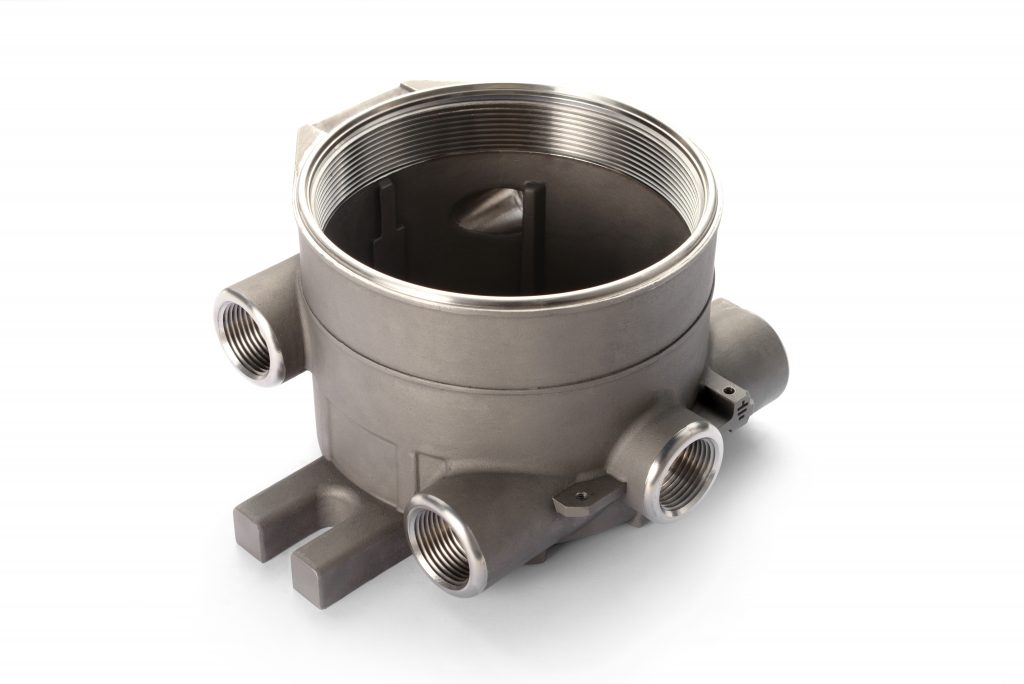
TCC is your reliable supplier for your precison cast parts. Precision castings from our investment casting foundry will be the highest quality castings serving in your market. Our lost wax casting process provides a large freedom in both design and material choice for your desired products.
What’s more, our engineering departement will give you a complete casting proposal about product design, material choice, machining details, ect for your reference. Our business core is to provide quality precision castings with high working performance.
Precision Casting Benefits
Precision Casting VS Sand Casting
Sand casting is a casting process working by creating the cavity for casting by sand, and the sand shell will produce a rough shape. Normally the tolerances of sand casting is CT8-9, and the surface finish is around Ra25. So for sand cast products, the rough surface will may well quire more machining operations than investment castings.
Precision casting creats desired shapes by a ceramic shell, and can produce much better surface finish product. We can meet a tight tolerance CT4-6 as precise as possible, thus to reduce net shape products and likely avoid further machining.
Precision Casting VS Machining
For some easy products with simple shape, we may chooice either precision casting or machining. Machining is the process that machining a part into final dimensions from bar directly. This will cause a large waste of raw material, which will imperceptibly add the production cost. Besides, if the quantity is large, the single production will longer the production time, which will delay the lead time.
Precision Casting makes a product to be costly in further machining. TCC casting has both casting workshop as well as machining shop. We can supply machined precision castings in a best price, but allowing our customers to receive well performed products that can put into application directly.
Precision Casting VS Precision Forging
Precision forging is the metal forming process that press hot or cold metal bars into shapes directly. To withstand high pressure, there is a high requirement on the material of forging dies. Commonly used material of forging dies is tool die, whose cost is quite high. The high cost tooling cost makes precision forging process not competitive as precision casting. Also precision forging has a district control on the shapes of products.
By comparision, precision casting require less tooling cost, and has no limitation on the dimensions of products. This makes our company available for all metal products.
Precision Casting VS Metal Fabrication
Metal fabrication is the process by cutting and bending metal plates into different shapes and thickness, and welding them together to form a product. This will cost more larbour cost and production time.
Precision Casting can greatly reduce the production time by attaching multiple wax models to a gate or system.