Microarc Oxidation( MAO) VS Anodic oxidation
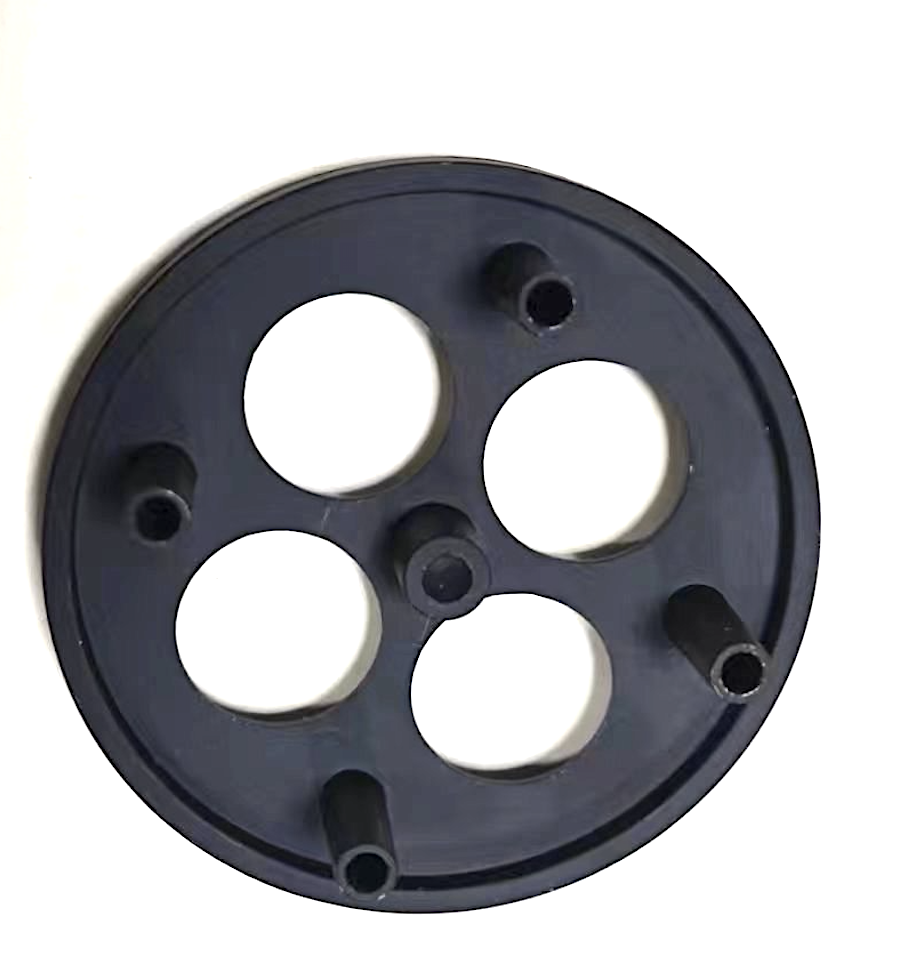
Microarc Oxidation( MAO), It is also been called Plasma electrolytic oxidation(PEO) or Microplasma oxidation(MPO ).It is a high technology of in-situ growing ceramic layer on the surface of aluminum, magnesium, titanium and other metals and their alloys .
The characteristics of micro-arc oxidation
•(1) The appearance of the ceramic membrane layer is uniformly dense and the combination is firm. It is matte and the color is consistent. The thickness of the film can be controllable from 10UM to 300UM;
•(2) Good wear resistance; The Hardness is HVA400 to 2500, the highest to 3000HV; The wear resistance is improved to 30% than the original material.
•(3) Good heat resistance. High temperature impact resistance of 2500°C for 20 seconds (the matrix melts and the ceramic layer is intact after 20 seconds) with strong flexibility , even the matrix is bending, The ceramic layer does not crack or fall off during fracture .
•(4) Strong corrosion resistance. The salt spray test >1000 hours.
•(5) Good insulation performance, electrical breakdown strength 5KV/mm, electrical .
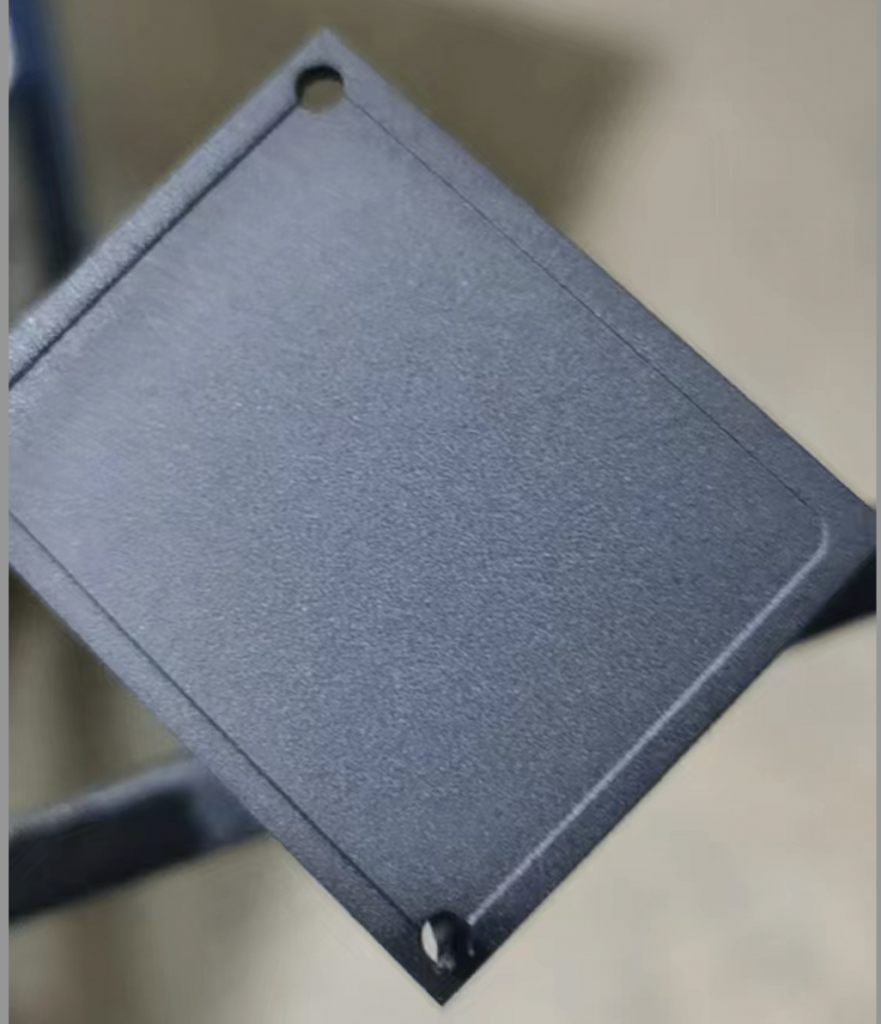
Microarc Oxidation VS Anodic oxidation
Specification | Microarc Oxidation | Anodic oxidation |
Working time(min ) | 10-30 | 30-60 |
Thickness of film(um ) | 10-300 | 30-60 |
Hardness(HV) | 1500-2500 | 300-400 |
Surface Porosity(%) | 0-40 | >40 |
Insulativity | good | uninsulation |
Solution PH | neutral or alkaline | acidic |
Flexibility | Good | Fragile |
Uniformity | Uniform on an internal and external surface. | Relatively uniform |
Wear resistance | Good | Poor |
Process flow | deoiling – Microarc oxidation – sealing | Alkali etching – pickling – chemical polishing – anodizing – sealing |
Working temperature(°C) | 10-90 | 13-26 |
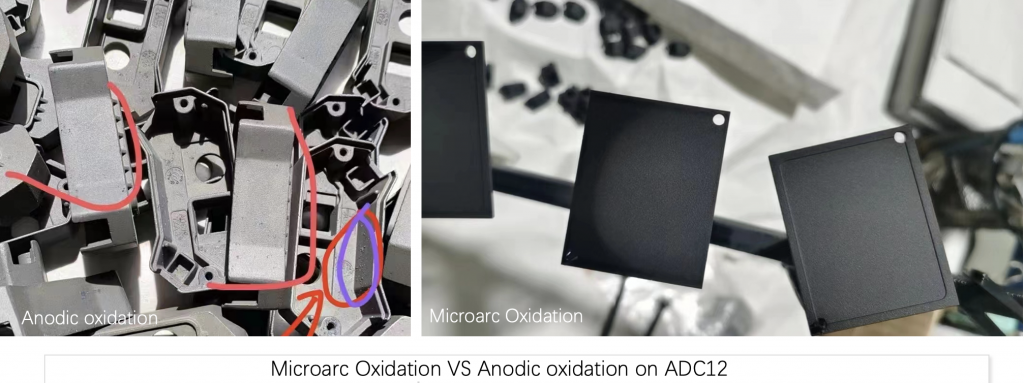
TCC has experienced with surface treatment on on the Aluminum with high content of Silicon, eg. ADC12 and A380. If you have such requirement , please contact us by email .