Gravity Die Casting VS Pressure Die Casting

There are two main processes which is gravity die casting and pressure die casting for Aluminum alloy .
What is the Gravity Die Casting?
Gravity Die Casting ( called Permanent Mold Casting in USA and Canada)is a permanent mold casting process , where the molten metal is poured from a vessel or ladle into the mold. The mold cavity fills with no force other than gravity, filling can be controlled by tilting the die. Undercuts, and cavities can be incorporated into the component form with the use of sand cores.
It specifically refers to metal casting, however, sand casting, metal casting, investment casting, lost mold casting can also be included generally .
Advantages of Gravity Die casting
-Less pores and can be heat treated.
-Low density
-Product finish is not high.
-Low production efficiency.
-Molding with long lifetime and low cost
-Simple technic process
-Not suitable for parts with thinner wall.
What is the Pressure Die Casting?
Pressure Die casting includes high pressure casting and low pressure casting.
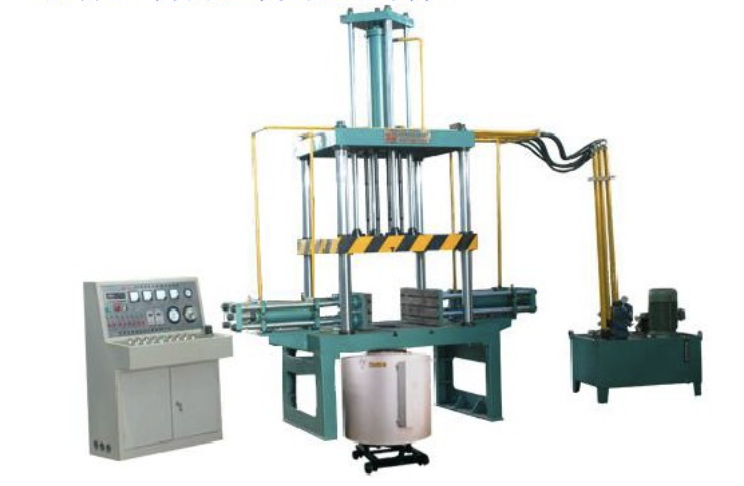
Low-pressure die casting is a method of production that uses pressure – rather than gravity – to fill molds with molten metal such as aluminum and magnesium. In this process, the holding furnace is located below the cast and the liquid metal is forced upwards through a riser tube and into the cavity. The pressure is applied constantly, sometimes in increasing increments, to fill the mold and hold the metal in place within the die until it solidifies. Once the cast has solidified, the pressure is released and any residual liquid in the tube or cavity flows back into the holding furnace for “recycling.” When cooled, the cast is simply removed.
Advantages of Low-Pressure Die Casting
-Precise control of the filling process.
-Reduces oxide formation and porosity.
-Ensure superior consistency of the partsfrom top to bottom
-Exceptional density , strength values and excellent dimensional accuracy.
-Fit for parts with simpler, symmetrical forms, complex geometries
-Uncomplicated machinery and technology, well to automation.
High-Pressure Die Casting (HPDC) is an extremely efficient manufacturing method for producing various product forms. The process forces molten metal at high speed, and high pressure into a closed steel die cavity. The die has a stationary and moving half, both of which are mounted to the die casting machine’s platens. The die casting machine has an injection end that uses hydraulics and pressurized gas to move a piston forward, injecting the molten metal into the closed steel die. The die casting machine also has a clamping end that utilizes hydraulics and mechanical toggles to absorb the injection pressure and hold the die shut while the part solidifies. The process is capable of turning molten metal into a solid near-net-shape part in seconds.
Advantages of High-Pressure Die Casting
-Fast filling, high production efficiency.
-High compactness, high product strength and surface hardness, low elongation.
-Good surface finish, generally up to RA6.3 or even Ra1.6.
-Fit for Products with thin wall thickness (the thinnest to 0.5mm).
-Much gases in Internal , poor porosity .
-Not allow heat treatment, small machining allowance (better less than 0.25mm ).
-High cost and short time life for molding
Comparison For Gravity die casting, High- pressure and Low- pressure
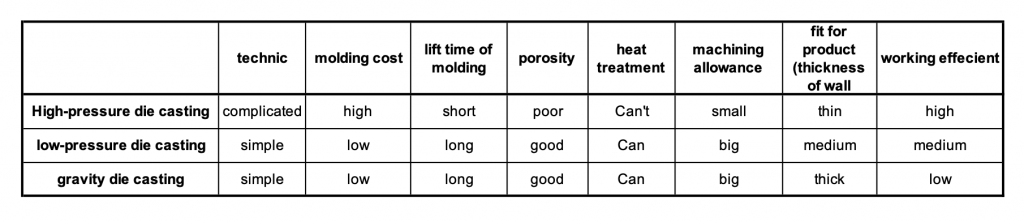
How and Which Die casting to choose, Gravity , High-pressure or Low-pressure die casting?
It mainly according to the wall thickness of the product:
As the high production efficiency ,the high- pressure die casting should be preferred priority if the production process and product performance can be met.
When the wall thickness of the product is over than 8mm, the high-pressure die-casting can not meet the expected requirement due to too many internal pores, the gravity die casting and low- pressure die casting can be considered.Generally ,low pressure casting is a compromise between high pressure casting and gravity casting.
TCC provide a complete manufacturing service solution for each project and application.For more information on Aluminum Gravity and Pressure Die Casting, please feel free to contact alina@tcc-casting.com.