WHAT’S THE DIFFERENCE ON MIM , COLD HEAD AND COLD EXTRUDING?
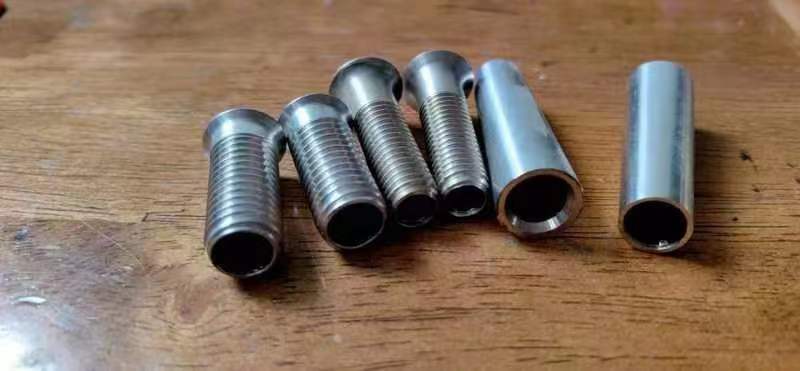
Which process is the most cost-effective for those small parts less than 50g, MIM , cold heading or cold extruding?
The cold heading process which is a branch of cold extrusion is most right way to manufacture the bolts, screws, nuts, nails, pins and other standard fasteners.
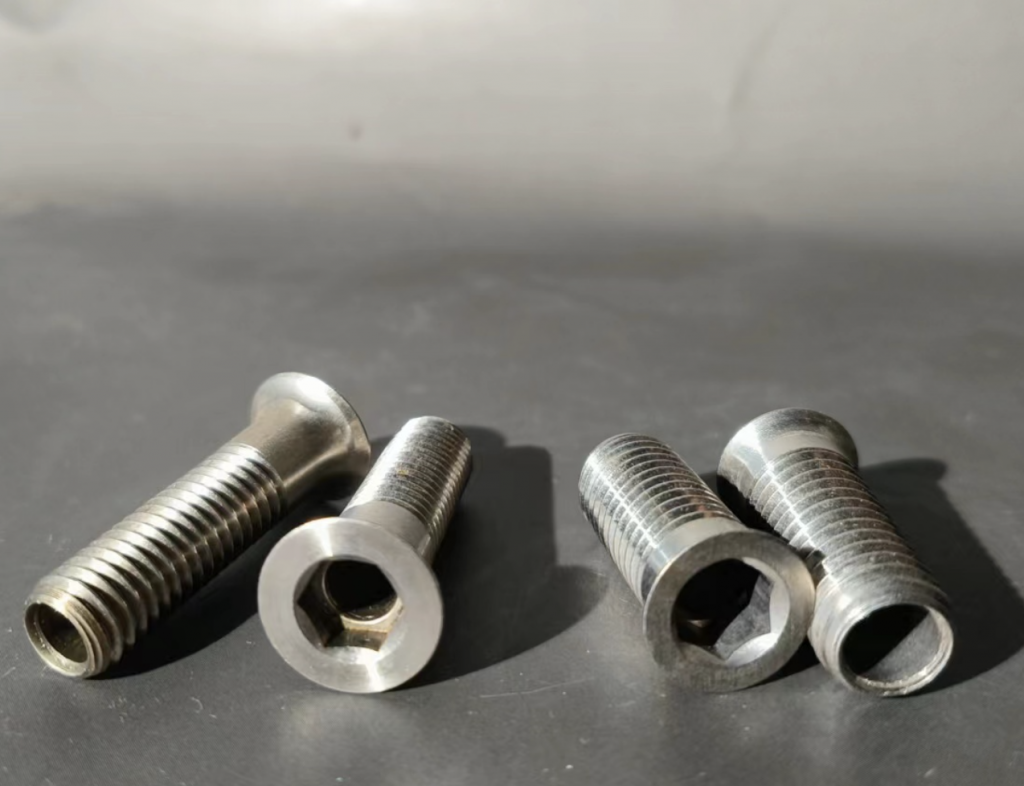
During the process of manufacturing bolts, the forming of the hexagonal head is made by cold heading, and the reduction of the rod part is cold extruding(extrusion). The non-cut hexagonal flange bolts (multi-station forming) are done by both cold heading and cold extruding, the hexagonal nut has only be done by cold heading before forming, and the extruding hole in the post process by cold extruding (positive and negative extrusion).
Cold heading process is a kind of processing method by the plastic deformation of the metal under the action of external force, and with the help of the mold, the volume of the metal is redistributed and transferred, so as to form the required parts or blanks.
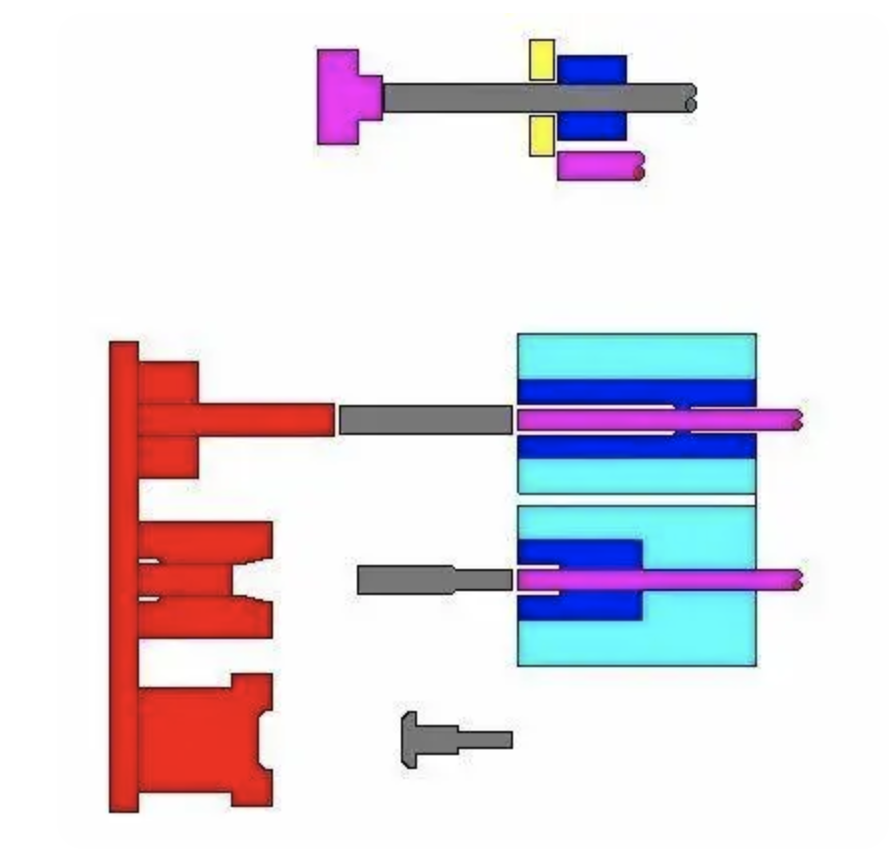
At present, cold extrusion technology has been widely used in fasteners, machinery, instruments, electrical appliances, light industry, aerospace, shipbuilding, military and other industrial sectors, and has gradually become the development direction of small and medium-sized forgings refined production.
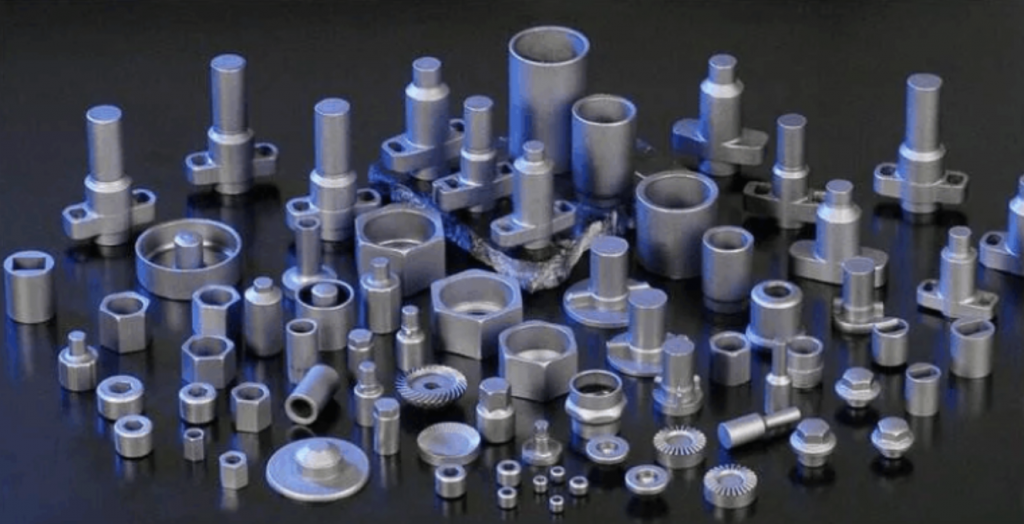
Cold extruding is the process by the metal blank in the cold extrusion cavity, at room temperature, through the press fixed punch to apply pressure to the blank, the metal blank produce plastic deformation and the processing method of parts. Cold extrusion is one of the machining processes of parts with no chips and less chips.
Cold extrusion is also divided into positive extrusion, reverse extrusion, composite extrusion, radial extrusion and so on.
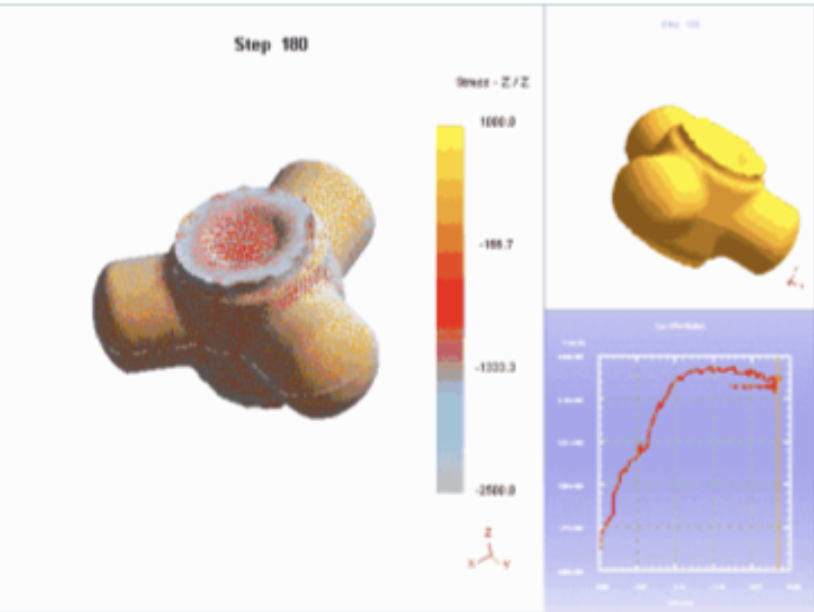
MIM (Metal Powder Injection Molding Technology), The injection molding process can directly form thin-wall and complex structural parts, and the shape of the product is close to the requirements of the final product, and the dimensional tolerance of the parts is generally maintained at about ±0.1-±0.3. In particular, it is of great significance to reduce the processing cost of cemented carbide, which is difficult to be machined, and to reduce the processing loss of precious metals.
MIM is suitable for mass production of parts. Due to the use of injection machine molding product blank, greatly improve the production efficiency and reduce the production cost.
MIM has wide range of applicable materials and application field (iron base, low alloy, high speed steel, stainless steel, hard alloy).

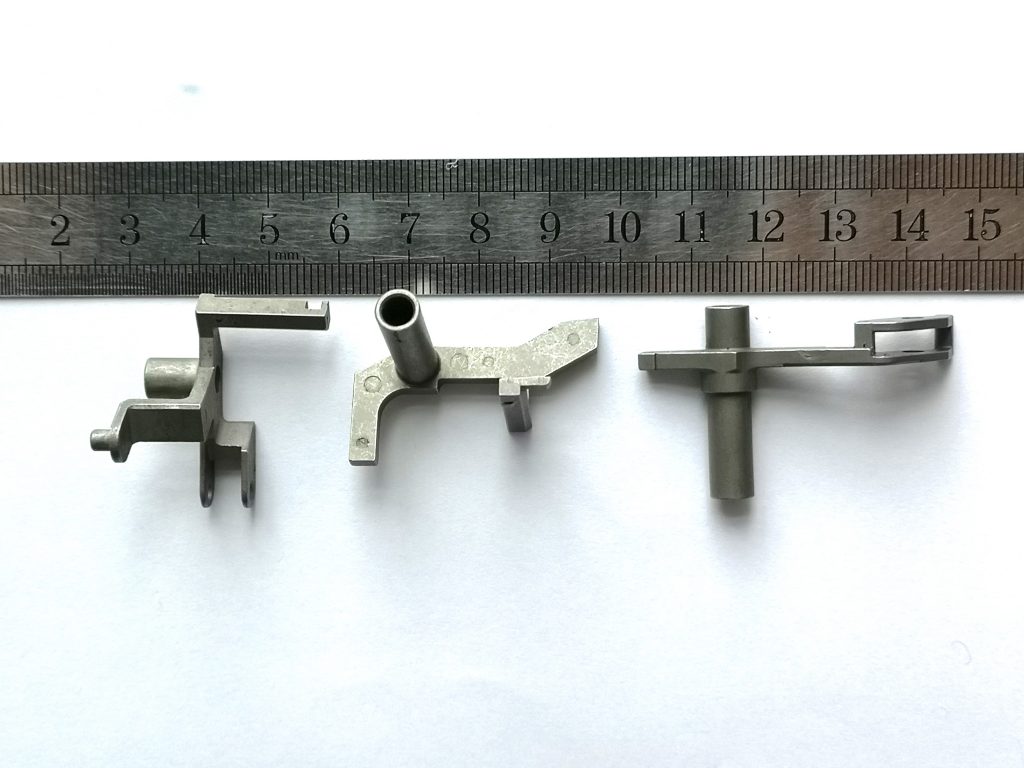
If you have some small parts and not sure which is the best way to manufacture , please feel free to contact Alina@tcc-casting